In the highly regulated and time-critical field of MRO in aviation, precision, coordination, and technical expertise are essential. When Elbe Flugzeugwerke (EFW) and Qantas needed reliable support for an Airbus A380 retrofit, they turned to ARTS Group. With over 25 years of experience across the entire aircraft lifecycle, we delivered a tailored work package focused on cabin interior modifications – a project that combined technical complexity with tight deadlines.
Scope of the A380 Retrofit: Focused MRO Aviation Support
In this retrofit project, ARTS Group was responsible for key interior refurbishment tasks on the A380:
- Removal, processing and reinstallation of economy class seats
- Carpet removal and replacement on the upper and lower decks
- Dismantling and installation of raceways (cable ducts in the floor)
These tasks were part of a larger cabin upgrade programme managed by EFW and Qantas. By outsourcing this defined work package to ARTS, both clients were able to shorten maintenance times while ensuring consistent quality across components.
Multidisciplinary Team with Aviation Expertise
The ARTS Group project team consisted of 15 specialists from across Europe, including aircraft mechanics, avionics technicians, coaters, plastics processors (CFRP/GRP), and interior fitters. Each team member received job-specific training prior to project start to meet EFW and Qantas’ technical and quality standards.
Our teams are built to match the complexity of each MRO aviation task — from structural work to systems integration. For this A380 retrofit, we combined multiple disciplines to ensure seamless execution across all phases.
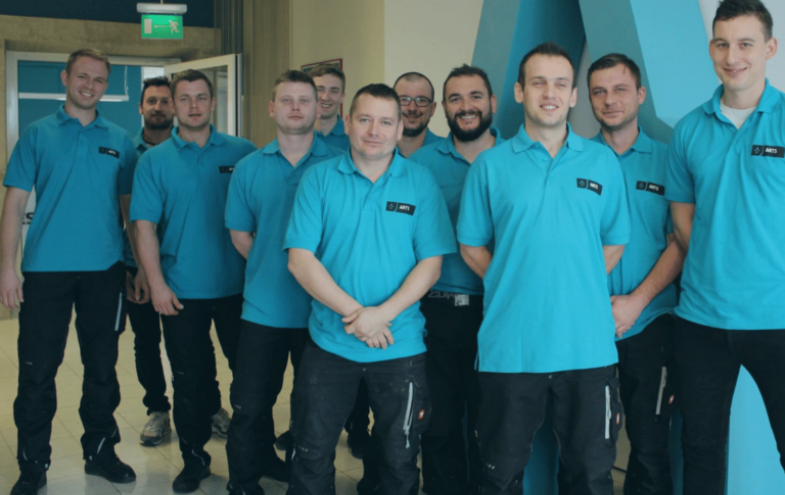
Seat Refurbishment: Component-Level Precision
Seats were removed from the aircraft and transported to one of ARTS Group's own facilities for detailed processing. The team handled:
- Replacement of seat cushions and covers
- Repair of sockets and AC connectors
- Light structural repairs depending on condition
Any additional defects were documented in defect reports and shared with the client. This allowed for fast, transparent decision-making – a critical factor in time-sensitive MRO aviation projects. The refurbished seats were then returned to the aircraft for reinstallation, meeting all functional and aesthetic requirements for long-haul passenger operations.
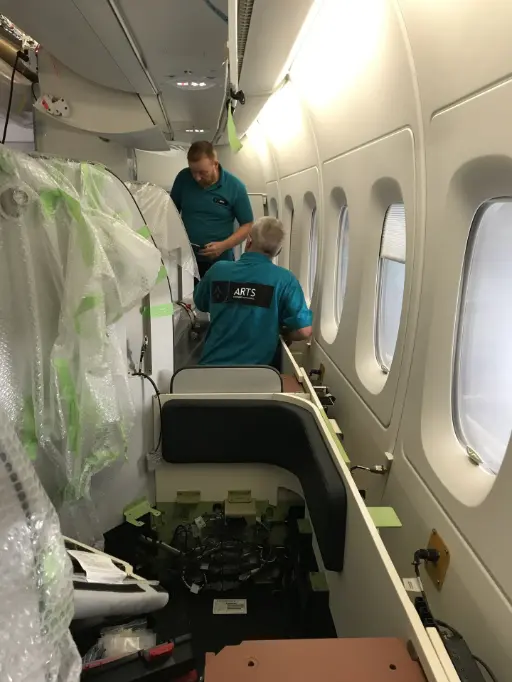
Carpet Work: Accuracy from Cut to Installation
While seat work was underway, another ARTS Group team removed the old carpets from both the upper and lower decks. For the upper deck, carpets were cut to size in ARTS Group’s Carpet Shop using customer-supplied drawings. For the lower deck, pre-cut kits were provided — though some on-site adjustments were necessary due to misfits.
Carpet installation in an aircraft the size of an A380 demands precision. A single incorrect cut can delay the entire project. That’s why ARTS applies strict quality checks before installation, reducing risk and avoiding rework on the aircraft.
Raceways: Safe and Efficient Cabling
As part of the floor renovation, the raceways — cable ducts used to route electrical systems — were also replaced. The team dismantled the existing units and installed new ones based on technical drawings. This required exact alignment with cable routing specifications to ensure safety and save space.
Correct raceway installation is essential in MRO aviation, not only from a safety perspective but also for maintenance access and long-term operability.
Planning, Communication, and Documentation
Before the project began, ARTS Group conducted an initial inspection of the aircraft to define the work scope, clarify technical requirements, and align on deadlines. This planning phase ensured that all resources and materials were in place ahead of time.
Work was tracked against a “Finding List”, which documented all agreed tasks and served as a transparent reference for both ARTS Group and the client. This approach avoided delays and reduced the need for reactive problem-solving during the retrofit.
All documentation and communication were handled in English — the standard language in aviation. This ensured that all team members and stakeholders were working from the same information, regardless of their location or native language.
International Teams, One Standard
The team for this A380 retrofit included technicians from Germany, England, and Poland. This diversity contributed to a solution-focused working culture, with each team member bringing experience and a different perspective to the job.
At ARTS Group, we view international project teams as a strength — especially in MRO aviation, where adaptability and cross-functional thinking are essential. All work followed internationally recognised aviation standards and was carried out under certified processes (EN 9100, ISO 9001, ISO 14001).
Why ARTS?
This project illustrates how ARTS Group operates in MRO aviation: structured, certified, and responsive. Our service model is built to integrate seamlessly into OEM and operator workflows by offering scalable support across the full aircraft lifecycle — from production and modification to maintenance and end-of-life.
We don’t just execute individual tasks. We take responsibility for defined work packages, manage sub-processes, and provide the technical depth needed for complex cabin, systems, and structural modifications. Whether it’s short-term deployment or long-term programme support, our teams work independently while remaining fully embedded in the client’s operations — on-site or remotely.
Our services go beyond cabin retrofits. Through our Mobile Aircraft Maintenance Crew, we deliver certified expertise worldwide for Line, Base, and Heavy Maintenance, AOG support, and component-level work such as modifications (AD/SBs), Non-Destructive Testing (NDT), and Borescope Inspections (BSI). In parallel, we offer technical aviation consulting, including FAL inspections, delivery support, and aircraft documentation reviews. Over 76% of our specialists bring more than 10 years of industry experience.
Our added value includes:
- Cross-functional teams with certified aviation skills — from mechanics to electronics, interiors to structures, tailored to project needs.
- Defined work packages with clear documentation — minimising interface risks and ensuring full traceability.
- Fast turnaround times and flexible deployment — thanks to optimised planning, scalable teams, and global mobility.
- Integration into OEM, MRO, and operator environments — with full compliance to ISO 9001, EN 9100, and ISO 14001 standards.
- Global delivery capability via our Mobile Aircraft Maintenance Crew — ensuring consistent support regardless of location or aircraft type.
With ARTS Group, customers gain a partner that understands operational realities and delivers technically sound, commercially efficient solutions — exactly what’s needed in today’s MRO aviation environment.
What This A380 Retrofit Says About How We Work
Retrofitting an aircraft as large as the Airbus A380 isn’t just about scale – it’s about managing complexity. Every modification must align with safety regulations, customer specifications, and operational timelines. That’s where ARTS Group comes in.
As a partner for MRO aviation projects, we deliver more than just manpower. We bring process reliability, aviation-grade quality, and a deep understanding of aircraft systems. The result: faster project execution, fewer disruptions, and a retrofit that meets every requirement.
Looking for a partner who delivers? ARTS Group supports your aircraft modification projects with precision, speed, and certified expertise. Contact us today.