Statistical Process Control (SPC) is being introduced into the A330 structural assembly process at Airbus Hamburg – with support from an ARTS Group expert working on-site. The goal: establish a scalable SPC approach that enhances process stability and improves quality in fuselage assembly.
Complexity in Airbus’ Decentralised Production Network
Unlike its competitor Boeing, which concentrates production in one location, Airbus spreads manufacturing across multiple European sites. Each plant has a specific responsibility: Hamburg handles fuselage and cabin production, Stade manufactures CFRP components and vertical stabilisers, Filton produces wing structures, and Bremen delivers high-lift systems. Final assembly for the A330 takes place in Toulouse.
This decentralised model requires tight coordination. Assembly tolerances are extremely narrow – even millimetre-level deviations at fuselage joints can introduce costly rework or alignment issues. That’s why Airbus is pushing for greater precision in early production stages. The aim: reduce downstream corrections and ensure process reproducibility.
SPC: A Proven Tool with Untapped Potential in Aviation
SPC is well established in other industries and already in use at Airbus for the A350 and A380 programs. The methodology, developed by Walter A. Shewhart, uses statistical analysis to monitor and control manufacturing processes. It enables early detection of deviations, reducing scrap and rework while increasing process transparency.
While SPC has clear benefits, its application in aviation remains limited – mainly due to low production volumes, which make it harder to build statistically significant datasets. Despite this, SPC has strong potential when applied strategically, especially in high-complexity areas like fuselage assembly.
Pilot Implementation: Section 16 at Location 601
ARTS Group is supporting Airbus with the SPC implementation for the A330 at building site 601 in Hamburg. This area handles the assembly of side shells, floor grids and bilge structures into the lower fuselage section 16 – which later connects to the center fuselage and wings.
Airbus monitors 30 parameters at this site. Photogrammetry is used for precision measurement of fuselage separation points. Small reflector plates are mounted at key points – such as outer skins, runways and seat rails – and measured at defined angles and distances. The focus is on the runways, as these show the widest tolerance range.
Measurements are captured using Bluetooth-enabled calipers, laser distance meters and other tools, and transferred directly to a tablet interface used by the assembly team. Once saved, the data is available for analysis. This enables clear correlation between process changes – for example, minor adjustments in part positioning – and their effect on product quality.
Alerts are also triggered when product data deviates from defined thresholds. In addition to SPC, the data supports mandatory Ground Test Instructions (GTIs), such as checks on ventilation and hydraulic systems.
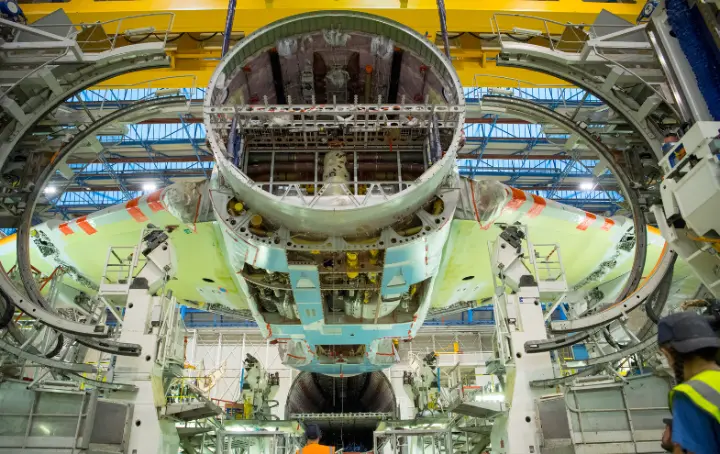
Looking Ahead: Towards More Intelligent Assembly
In the future, SPC could enable more adaptive assembly processes. For example, suppliers might provide detailed “digital records” for components. These would include process histories and target values, helping production teams align tolerances at each step with greater precision. Instead of working within tolerance bands, teams would target exact values – improving overall quality and reducing variation.
This shift would align with modern quality concepts, where the goal is not just staying within limits, but achieving consistency across all stages of production.
ARTS Group: Driving Operational Excellence in Aerospace
By embedding experienced specialists directly at the point of need, ARTS Group provides OEM support for aerospace manufacturers like Airbus in tackling complex production challenges. Whether through process optimisation, quality consulting or hands-on industrial support, our goal is to make aviation manufacturing more efficient, predictable and scalable.