Die Luftfahrt von morgen gestalten
Mit über 25 Jahren Erfahrung ist die ARTS Group Ihr verlässlicher Partner für Aircraft Related Technical Services.
Wir bieten maßgeschneiderte Lösungen über den gesamten Lebenszyklus eines Flugzeugs an.
ARTS Group - Extending Your Success
Die ARTS Group ist mehr als nur ein Dienstleister. Wir sind Ihr Partner, der Sie dabei unterstützt, die Herausforderungen der Luftfahrtbranche zu meistern. Dank unserer mehr als 25-jährigen Branchenerfahrung bieten wir Ihnen maßgeschneiderte Lösungen für den gesamten Lebenszyklus eines Fluggerätes: von der Fertigung über Wartung und Betrieb bis hin zu End-of-Life Strategien.
Unsere nach ISO 9001 und EN 9100 zertifizierten Prozesse gewährleisten Exzellenz in den Bereichen Fertigung, Aviation Consulting sowie der Bereitstellung von Teilen und Komponenten. So ermöglichen wir eine nahtlose Prozessoptimierung, Workforce Scalability und Ressourceneffizienz, um Ihre sich wandelnden Anforderungen zu erfüllen. Ob durch OEM Support, Aviation Asset Management oder Workforce Solutions – wir fördern Qualität, Effizienz und Nachhaltigkeit in jedem Projekt.
25
Jahre Luftfahrterfahrung
~ 1 Mio.
Geleistete Projektstunden in der Luftfahrt
~500
erfahrene Mitarbeitende
43
zufriedene Luftfahrtkunden
ARTS Group - Extending Your Success
Die ARTS Group ist mehr als nur ein Dienstleister. Wir sind Ihr Partner, der Sie dabei unterstützt, die Herausforderungen der Luftfahrtbranche zu meistern. Dank unserer mehr als 25-jährigen Branchenerfahrung bieten wir Ihnen maßgeschneiderte Lösungen für den gesamten Lebenszyklus eines Fluggerätes: von der Fertigung über Wartung und Betrieb bis hin zu End-of-Life Strategien.
Unsere nach ISO 9001 und EN 9100 zertifizierten Prozesse gewährleisten Exzellenz in den Bereichen Fertigung, Aviation Consulting sowie der Bereitstellung von Teilen und Komponenten. So ermöglichen wir eine nahtlose Prozessoptimierung, Workforce Scalability und Ressourceneffizienz, um Ihre sich wandelnden Anforderungen zu erfüllen. Ob durch OEM Support, Aviation Asset Management oder Workforce Solutions – wir fördern Qualität, Effizienz und Nachhaltigkeit in jedem Projekt.
25
Jahre Luftfahrterfahrung
~ 1 Mio.
Geleistete Projektstunden in der Luftfahrt
~500
erfahrene Mitarbeitende
43
zufriedene Luftfahrtkunden
Unsere Services
OEM Support
Als Ihr Outsourcing-Partner in der Luftfahrt unterstützt die ARTS Group Sie dabei, Fertigungskosten, Produktionszeiten und Kapazitätsaufwände zu reduzieren – mit maßgeschneiderten Lösungen, die Ihre Prozesse optimieren und gleichzeitig höchste Qualitätsstandards in der Luftfahrtfertigung einhalten.
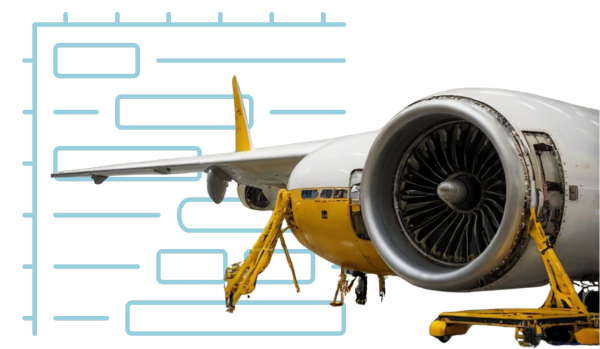
Mehr Erfahren
Aviation Asset Management
Wir bieten ein umfassendes Spektrum an weltweiten Aviation Asset Management Lösungen, egal ob für Operator, Lessor oder Owner. Als Erweiterung Ihres technischen Teams entwickeln wir individuelle Strategien, die die Kosteneffizienz Ihrer Flotte verbessern und die Einsatzbereitschaft über den gesamten Lebenszyklus des Fluggerätes hinweg sicherstellen.
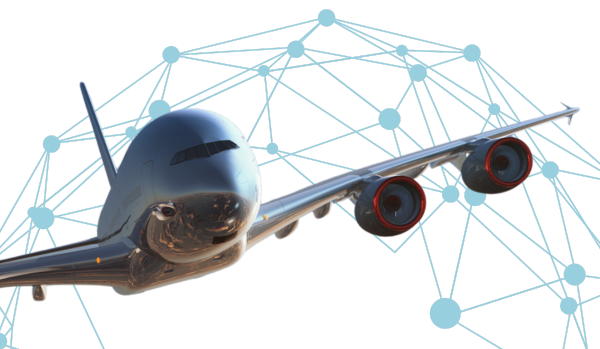
Mehr Erfahren
Workforce Solutions
Die ARTS Group bietet individuell zugeschnittene Workforce Solutions, mit denen unsere Kunden ihre Prozesse optimieren, die Effizienz steigern und höchste Qualitätsstandards aufrechterhalten können. Ob durch Aviation Recruiting Services oder temporäre Manpower – wir passen uns Ihren speziellen Anforderungen an und sichern reibungslose Abläufe.
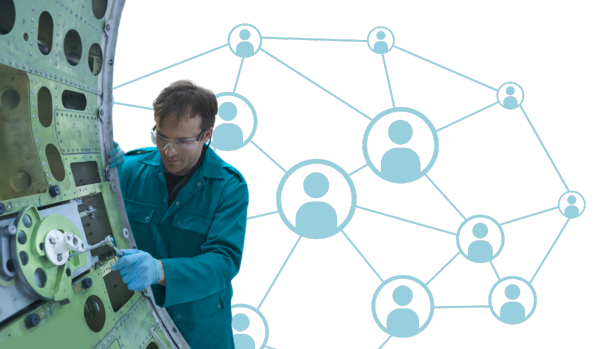
Mehr Erfahren
Unsere Services
OEM Support
Als Ihr Outsourcing-Partner in der Luftfahrt unterstützt die ARTS Group Sie dabei, Fertigungskosten, Produktionszeiten und Kapazitätsaufwände zu reduzieren – mit maßgeschneiderten Lösungen, die Ihre Prozesse optimieren und gleichzeitig höchste Qualitätsstandards in der Luftfahrtfertigung einhalten.
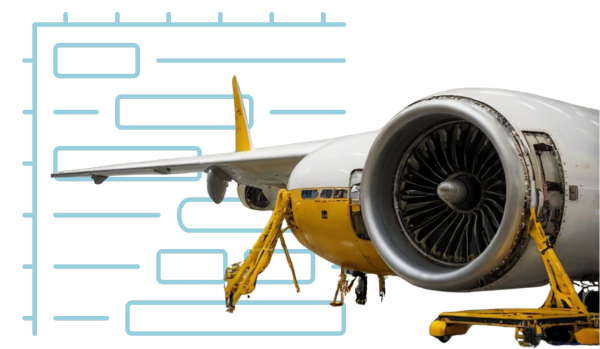
Mehr Erfahren
Aviation Asset
Management
Wir bieten ein umfassendes Spektrum an weltweiten Aviation Asset Management Lösungen, egal ob für Operator, Lessor oder Owner. Als Erweiterung Ihres technischen Teams entwickeln wir individuelle Strategien, die die Kosteneffizienz Ihrer Flotte verbessern und die Einsatzbereitschaft über den gesamten Lebenszyklus des Fluggerätes hinweg sicherstellen.
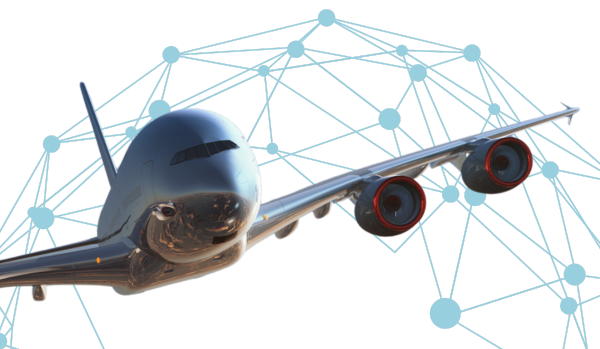
Mehr Erfahren
Workforce Solutions
Die ARTS Group bietet individuell zugeschnittene Workforce Solutions, mit denen unsere Kunden ihre Prozesse optimieren, die Effizienz steigern und höchste Qualitätsstandards aufrechterhalten können. Ob durch Aviation Recruiting Services oder temporäre Manpower – wir passen uns Ihren speziellen Anforderungen an und sichern reibungslose Abläufe.
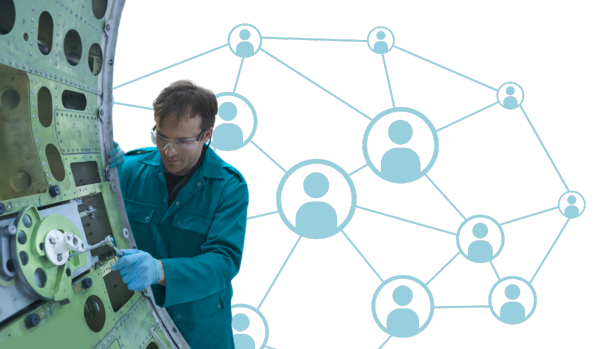
Mehr Erfahren
Unsere Kunden
Unsere Kunden
OEMs
Wir unterstützen globale und lokale Hersteller im Projektmanagement, Supply Chain Management und in der Logistik sowie mit temporären Personallösungen und industriellem Produktsupport. So helfen wir ihnen, ihre Abläufe zu optimieren und innovative Lösungen umzusetzen.
MROs
MROs stehen unter ständigem Druck, die Ausfallzeiten von Flugzeugen zu minimieren und gleichzeitig höchste Sicherheitsstandards einzuhalten. Sie verlassen sich auf uns für zuverlässige Wartungsunterstützung, Workforce Solutions, Aviation Consulting sowie den Handel mit Ersatzteilen und Material.
Operators
Fluggesellschaften und andere Betreiber benötigen flexible Lösungen im Aviation Asset Management und in der Flugzeugwartung, um einen reibungslosen Betrieb sicherzustellen – insbesondere bei AOG-Situationen. Zusätzlich bieten wir Inspektionssupport, den Handel mit Ersatzteilen und Material sowie Aviation Consulting.
Lessors
Unsere Kunden konzentrieren sich darauf, den Wert und die Verfügbarkeit ihrer Flugzeugflotten zu maximieren. Sie setzen auf unsere Expertise in der technischen Beratung, bei Inspektionen und im Aviation Asset Management, um die Betriebsbereitschaft und Rentabilität sicherzustellen.
MROs
MROs stehen unter ständigem Druck, die Ausfallzeiten von Flugzeugen zu minimieren und gleichzeitig höchste Sicherheitsstandards einzuhalten. Sie verlassen sich auf uns für zuverlässige Wartungsunterstützung, Workforce Solutions, Aviation Consulting sowie den Handel mit Ersatzteilen und Material.
OEMs
Wir unterstützen globale und lokale Hersteller im Projektmanagement, Supply Chain Management und in der Logistik sowie mit temporären Personallösungen und industriellem Produktsupport. So helfen wir ihnen, ihre Abläufe zu optimieren und innovative Lösungen umzusetzen.
Unsere Kunden
Unsere Kunden
OEMs
Wir unterstützen globale und lokale Hersteller im Projektmanagement, Supply Chain Management und in der Logistik sowie mit temporären Personallösungen und industriellem Produktsupport. So helfen wir ihnen, ihre Abläufe zu optimieren und innovative Lösungen umzusetzen.
MROs
MROs stehen unter ständigem Druck, die Ausfallzeiten von Flugzeugen zu minimieren und gleichzeitig höchste Sicherheitsstandards einzuhalten. Sie verlassen sich auf uns für zuverlässige Wartungsunterstützung, Workforce Solutions, Aviation Consulting sowie den Handel mit Ersatzteilen und Material.
Operators
Fluggesellschaften und andere Betreiber benötigen flexible Lösungen im Aviation Asset Management und in der Flugzeugwartung, um einen reibungslosen Betrieb sicherzustellen – insbesondere bei AOG-Situationen. Zusätzlich bieten wir Inspektionssupport, den Handel mit Ersatzteilen und Material sowie Aviation Consulting.
Lessors
Unsere Kunden konzentrieren sich darauf, den Wert und die Verfügbarkeit ihrer Flugzeugflotten zu maximieren. Sie setzen auf unsere Expertise in der technischen Beratung, bei Inspektionen und im Aviation Asset Management, um die Betriebsbereitschaft und Rentabilität sicherzustellen.
MROs
MROs stehen unter ständigem Druck, die Ausfallzeiten von Flugzeugen zu minimieren und gleichzeitig höchste Sicherheitsstandards einzuhalten. Sie verlassen sich auf uns für zuverlässige Wartungsunterstützung, Workforce Solutions, Aviation Consulting sowie den Handel mit Ersatzteilen und Material.
OEMs
Wir unterstützen globale und lokale Hersteller im Projektmanagement, Supply Chain Management und in der Logistik sowie mit temporären Personallösungen und industriellem Produktsupport. So helfen wir ihnen, ihre Abläufe zu optimieren und innovative Lösungen umzusetzen.
Sprechen Sie uns an!
Sie stehen vor akuten Herausforderungen oder haben spezifische Anforderungen?
Warten Sie nicht – sprechen Sie uns an.
Unsere erfahrenen Expert:innen bieten Ihnen gern ein unverbindliches Erstgespräch an, in dem wir gemeinsam passgenaue Lösungen für Ihre Situation erarbeiten – effizient, zertifiziert und auf Sie zugeschnitten.
KontaktSie stehen vor akuten Herausforderungen oder haben spezifische Anforderungen?
Warten Sie nicht – sprechen Sie uns an.
Unsere erfahrenen Expert:innen bieten Ihnen gern ein unverbindliches Erstgespräch an, in dem wir gemeinsam passgenaue Lösungen für Ihre Situation erarbeiten – effizient, zertifiziert und auf Sie zugeschnitten.
KontaktWorkforce Solutions
Door Modification A380
Einblicke in unsere Projekte
Non-Destructive Testing Pliatus PC 24 und Airbus 220
Quality Consulting
OEM Working Party
Einblicke in unsere Projekte
Strata
Quality Consulting
ATR
OEM Working Party
Warum ARTS Group?
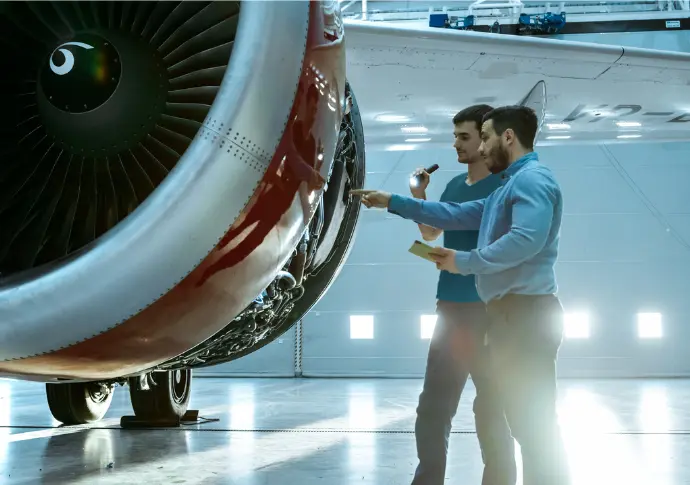
Karriere bei der ARTS Group
Entdecken Sie vielfältige Karrieremöglichkeiten in der Luftfahrt bei der ARTS Group. Werfen Sie einen Blick auf unsere offenen Positionen und gestalten Sie Ihre berufliche Zukunft mit uns – ob im technischen Bereich, im Projektmanagement oder in der Beratung.
Jetzt Job Finden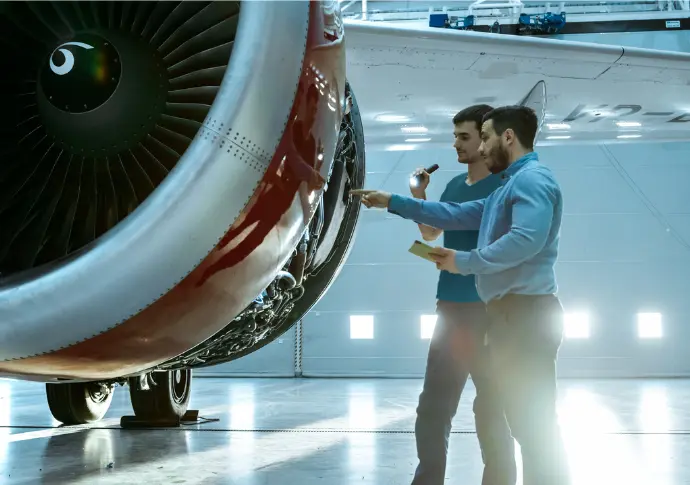
Karriere bei der ARTS Group
Entdecken Sie vielfältige Karrieremöglichkeiten in der Luftfahrt bei der ARTS Group. Werfen Sie einen Blick auf unsere offenen Positionen und gestalten Sie Ihre berufliche Zukunft mit uns – ob im technischen Bereich, im Projektmanagement oder in der Beratung.
Jetzt Job FindenInternationale Standorte
ARTS Group in Frankreich
Toulouse ist ein zentraler Standort der europäischen Luftfahrtindustrie. Unser Büro befindet sich strategisch günstig in einem Hangar auf dem Flughafengelände und bietet uns unmittelbaren Zugang zu den OEM-Betrieben. Diese vorteilhafte Lage ermöglicht unseren Kunden einen direkten Zugang zu den Hangar-Facilities.
ARTS Group in Deutschland
Deutschland ist die Heimat der ARTS Group. Mit Büros in Hamburg und Dresden sind wir in zwei bedeutenden Luftfahrtzentren vertreten. Beide Standorte zeichnen sich durch hohe Innovationskraft und Qualitätsorientierung aus.
ARTS Group in VAE
Unsere Niederlassung in Dubai ist ein zentraler Baustein unserer internationalen Wachstumsstrategie. Dank der günstigen Lage am Schnittpunkt von Europa, Asien und Afrika bietet sie direkten Zugang zu einem der dynamischsten Luftfahrtmärkte weltweit – ein bedeutender Vorteil für unsere Kunden vor Ort.
ARTS Group in Frankreich
Toulouse ist ein zentraler Standort der europäischen Luftfahrtindustrie. Unser Büro befindet sich strategisch günstig in einem Hangar auf dem Flughafengelände und bietet uns unmittelbaren Zugang zu den OEM-Betrieben. Diese vorteilhafte Lage ermöglicht unseren Kunden einen direkten Zugang zu den Hangar-Facilities.
ARTS Group in Deutschland
Deutschland ist die Heimat der ARTS Group. Mit Büros in Hamburg und Dresden sind wir in zwei bedeutenden Luftfahrtzentren vertreten. Beide Standorte zeichnen sich durch hohe Innovationskraft und Qualitätsorientierung aus.
ARTS Group in VAE
Unsere Niederlassung in Dubai ist ein zentraler Baustein unserer internationalen Wachstumsstrategie. Dank der günstigen Lage am Schnittpunkt von Europa, Asien und Afrika bietet sie direkten Zugang zu einem der dynamischsten Luftfahrtmärkte weltweit – ein bedeutender Vorteil für unsere Kunden vor Ort.
Kontaktieren Sie uns
Ob es um die Optimierung Ihrer Supply Chain, die Reduzierung von Flugzeugstillstandzeiten oder die Suche nach zertifizierten, nachhaltigen Lösungen geht – wir kennen die branchenspezifischen Anforderungen und liefern belastbare Antworten.
Frankreich
35, Rue Gabriel Clerc, H16B,
31700 Blagnac
Tel: +33 561 158 721
E-Mail: france@arts.aero
Deutschland
Hermann-Reichelt-Str. 3
Airport Center Dresden
01109 Dresden
Tel: +49 351 795 808 0
E-Mail: germany@arts.aero
Vereinigte Arabische Emirate
Office 510, 5th Floor, 8W Building
DAFZA, Dubai International Airport
Tel: +971 4 258 1099
E-Mail: dubai@arts.aero