La maîtrise statistique des processus (MSP) est actuellement introduit dans le processus d'assemblage structurel de l'A330 chez Airbus Hambourg, avec le soutien d'un expert du groupe ARTS qui travaille sur place. L'objectif : mettre en place une approche SPC évolutive qui augmente la stabilité des processus et améliore la qualité de l'assemblage du fuselage.
Complexité du réseau de production décentralisé d'Airbus
Contrairement à son concurrent Boeing, qui concentre sa production sur un seul site, Airbus répartit sa production sur plusieurs sites européens. Chaque usine a une tâche spécifique : Hambourg est responsable de la production du fuselage et de la cabine, Stade fabrique les composants en CFRP et les empennages latéraux, Filton produit les structures des ailes et Brême fournit les systèmes à haute portance. L'assemblage final de l'A330 a lieu à Toulouse.
Ce modèle décentralisé nécessite une coordination étroite. Les tolérances de fabrication sont extrêmement faibles : même des écarts de l'ordre du millimètre au niveau des raccords du fuselage peuvent entraîner des retouches coûteuses ou des problèmes d'alignement. C'est pourquoi Airbus vise une plus grande précision dans les premières phases de production. L'objectif : moins de corrections dans les phases ultérieures et une plus grande reproductibilité des processus.
MSP : un outil éprouvé au potentiel inexploité dans l'aéronautique
La MSP est déjà bien établi dans d'autres secteurs et est déjà utilisé chez Airbus pour les programmes A350 et A380. La méthodologie développée par Walter A. Shewhart utilise des analyses statistiques pour surveiller et contrôler les processus de fabrication. Elle permet de détecter rapidement les écarts, de réduire les rebuts et les retouches, tout en augmentant la transparence des processus.
Bien que la MSP offre des avantages évidents, son utilisation dans l'aéronautique reste limitée, principalement en raison des faibles volumes de production qui rendent plus difficile la création d'ensembles de données statistiquement significatifs. Néanmoins, le SPC présente un grand potentiel lorsqu'il est utilisé de manière stratégique, en particulier dans des domaines très complexes tels que l'assemblage de fuselages.
Mise en œuvre pilote : section 16 sur le site 601
Le groupe ARTS soutient Airbus dans la mise en œuvre de la MSP pour l'A330 sur le site de construction 601 à Hambourg. Dans cette zone, les coques latérales, les grilles de plancher et les structures de cale sont assemblées pour former la partie inférieure du fuselage 16, qui sera ensuite reliée au fuselage central et aux ailes.
Airbus surveille 30 paramètres sur ce site. La photogrammétrie est utilisée pour mesurer avec précision les points de séparation du fuselage. De petites plaques réfléchissantes sont fixées à des points importants, tels que le revêtement extérieur, les chemins de roulement et les rails de siège, et mesurées à des angles et des distances définis. L'accent est mis sur les chemins de roulement, car ceux-ci présentent la plus grande plage de tolérance.
Les mesures sont enregistrées à l'aide de pieds à coulisse compatibles Bluetooth, de télémètres laser et d'autres outils, puis transmises directement à une interface tablette utilisée par l'équipe d'assemblage. Une fois enregistrées, les données sont disponibles pour analyse. Cela permet d'établir une corrélation claire entre les modifications du processus, par exemple les ajustements mineurs du positionnement des pièces, et leur impact sur la qualité du produit.
De plus, des alertes sont déclenchées lorsque les données du produit s'écartent des seuils définis. En plus du SPC, les données prennent en charge les instructions de test au sol obligatoires (GTI), telles que les vérifications des systèmes de ventilation et hydrauliques.
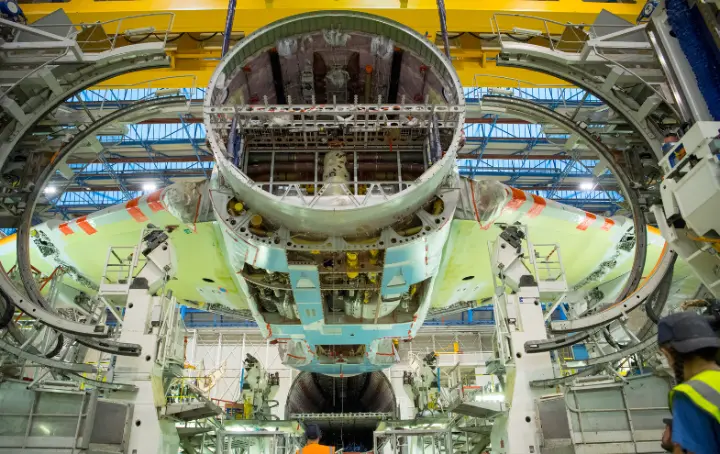
Perspectives : vers un assemblage plus intelligent
À l'avenir, la MSP pourrait permettre des processus d'assemblage plus adaptatifs. Par exemple, les fournisseurs pourraient fournir des « enregistrements numériques » détaillés pour les composants. Ceux-ci contiendraient l'historique des processus et les valeurs cibles et aideraient les équipes de production à aligner plus précisément les tolérances à chaque étape. Au lieu de travailler dans des plages de tolérance, les équipes viseraient des valeurs exactes, ce qui améliorerait la qualité globale et réduirait les écarts.
Ce changement serait conforme aux concepts de qualité modernes, dont l'objectif n'est pas seulement de rester dans les limites, mais d'atteindre une cohérence à toutes les étapes de la production.
ARTS Group : promouvoir l'excellence opérationnelle dans l'aéronautique
En intégrant des spécialistes expérimentés directement sur le terrain, ARTS Group aide les équipementiers aéronautiques tels qu'Airbus à relever des défis de production complexes. Que ce soit par l'optimisation des processus, le conseil en matière de qualité ou l'assistance industrielle pratique, notre objectif est de rendre la production aéronautique plus efficace, plus prévisible et plus évolutive.